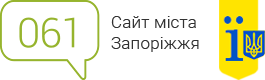
Как на «Запорожстали» железную руду превращают в сталь: экскурсия на производство, — ФОТОРЕПОРТАЖ

В новом спецпроекте 061 продолжает рассказывать, как на запорожских предприятиях создают те или иные продукты. Ранее наши корреспонденты показывали производства кваса, пива и шифера. В этот раз 061 побывал на металлургическом комбинате «Запорожсталь» и увидел, как железная руда превращается в рулоны и листы стали.
Производство металлопроката на «Запорожстали», если очень упростить, работает по следующей схеме. Сначала на аглофабрике из обогащенного железорудного концентрата, железной руды и других материалов изготавливают агломерат. Его загружают с другими материалами в доменные печи для получения чугуна. Чугун вместе с добавками переплавляют в сталь в мартеновском цехе.
Затем полученную плавку разливают в слитки и отправляют в прокатное производство. Там горячий многотонный слиток на станах раскатывают до необходимых размеров. После охлаждения сталь упаковывают в рулоны или режут на листы, а затем — отправляют потребителю. Корреспонденты 061 посетили цеха «Запорожстали» и увидели все этапы производства.

Доменная печь: из руды – в чугун
Ежегодно «Запорожсталь» выплавляет больше 4 миллиона тонн чугуна. На металлургическом комбинате – 4 доменные печи. Домна, в которой происходит процесс выплавки, представляет собой вертикальную плавильную печь высотой около 70 метров.

Во время работы домны в печь регулярно добавляют новые порции железорудного агломерата вместе с коксом, окатышами и другими материалами.
Агломерат «готовят» в агломерационном цехе комбината. Его привозят к домнам железнодорожными составами и загружают в большие емкости – бункера доменной печи. Аналогично сюда привозят тонны еще одного ингредиента – кокса.
Шихту – смесь агломерата, окатышей, известняка и железной руды в определенных пропорциях, и кокса – слоями загружают в доменную печь с помощью движущейся 25-тонной вагонетки – скипа. В сутки для производства более 3 тысяч тонн чугуна приблизительно тратят 4,3 тысяч тонн агломерата, 1,5 тысячи тонн окатышей и 1,2 тысяч тонн кокса.

Плавка материалов происходит в нижней части печи благодаря выделению большого количества тепла при горении кокса в потоке нагретого до температуры 1100 градусов дутья – сжатого воздуха, обогащенного кислородом и углеводородным топливом. Горячий воздух подается внутрь через расположенные по радиусу доменной печи отверстия – фурмы. В качестве дополнительного топлива в доменном производстве «Запорожстали» в связи с экономией сейчас используют не природный газ, а пылеугольное топливо.
Расплавленные продукты плавки – чугун и шлак – накапливаются в нижней части доменной печи – горне. Когда приходит время, бригада горновых при помощи специальной машины вскрывает чугунную лётку – отверстие в печи: через него жидкий чугун и шлак стекают в желоб.
Затем плавка разделяется на чугун и шлак, которые разливается в разные ковши. Чугун отправляется в мартеновский цех, чтобы стать сталью.
За работой доменной печи следят в диспетчерской. Здесь на огромном экране отображается информация со всех датчиков и приборов: температура, состояние системы охлаждения, онлайн контроль за выбросами, показатели дутья, уровень расходуемого материала в печи и т.д.
Мартеновская печь: миксер, завалка и разливка
В мартеновском цехе чугун попадает в миксерное отделение. Здесь в огромной 1300-тонной бочке смешиваются плавки из разных доменных печей комбината – для усреднения температуры и химического состава.
Сначала в сталеплавильную печь загружают металлолом, затем заливают жидкий чугун. Химическая реакция нагревает металл и расплавляет лом в течении нескольких часов.
Когда плавка готова, происходит выпуск стали в сталеразливочные ковши – емкостью 250 тонн. Из ковшей сталь разливают в слитки массой до 18,6 тонн каждый. Горячим металлом наполняют специальные емкости – изложницы, в которые добавляют алюминий для улучшения качества продукта.
После этого изложницы со сталью отправляются на следующий этап производства – в обжимной цех.
За день в мартеновском цеху производят в среднем 11 тысяч тонн стали. Ежегодное производство составляет около 4 миллионов тонн.

Обжимной цех: нагрев и слябинг
В обжимном цехе слитки снимают с железнодорожных составов и отправляют их в специальные печи – нагревательные колодцы.

В нагревательных колодцах остывшие во время транспортировки слитки нагреваются до нужной температуры перед прокаткой на обжимном стане – «Слябинге-1150».
На стане «Слябинг-1150» 16-тонный слиток стали размером 780 (толщина) на 1400 (ширина) миллиметров «обжимают» до нужных размеров. С помощью четырех прокатных валков слиток «прокатывают» по вертикали и горизонтали. Почти за две минуты слиток превращается в сляб – плиту толщиной 150 мм, шириной до 1500 мм и длиной до 12 метров.
В обжимном цехе за час могут «раскатать» порядка 600 тонн стали.
После этого горячие слябы направляются в цех горячей прокатки тонкого листа.
Цех горячей прокатки: 700-метровая полоса горячего металла
В цехе горячей прокатки тонкого листа на прокатном стане непрерывно производят горячекатаные полосы толщиной от 1,5 мм до 10 мм, шириной от 860 до 1500 мм.
Горячая полоса проходит 10 клетей черновой и чистовой группы для обжатия. В каждой клети по четыре валка. С каждой парой валков раскат после обжатий становится тоньше и длиннее при той же ширине. 4 клети черновой группы раскат проходит при температуре около 1100 градусов Цельсия.
На финальном этапе полосу после охлаждения водой сматывают в рулоны. Даже после охлаждения и смотки температура рулона – порядка 600 градусов. Масса рулона металла может составлять до 16 тонн.
На наших глазах сляб массой 14 тонн «раскатали» в полосу и толщиной 2 миллиметра и длиной около 600 метров. Максимально длина полосы стали на этом стане может достигать 700 метров.
В среднем, каждый час в этом цеху «прокатывают» 480 тонн стали. Годовое производство – порядка 3,6 миллиона тонн.
Цех холодной прокатки: удалить окалину и сделать металл тоньше
Поступающие в цех холодной прокатки горячекатаные рулоны направляются на склад для остывания до необходимой температуры. Во время горячей прокатки и остывания на поверхности металла образуется окалина – соединение оксида железа. Задача травильного отделения цеха холодной прокатки – удалить эту окалину: сначала механическим способом, а потом – химическим (соляной кислотой).
Для непрерывности производственного процесса рулоны в травильной линии разматывают и сваривают в «бесконечную» полосу. Затем «бесконечная» полоса попадает в ванны с кислотой, после чего моется, сушится и снова сматывается в рулоны.
Новые технологии позволили полностью ликвидировать сбросы химии в Днепр: сейчас кислоты рециркулируются и повторно используются в производстве.
После травильного отделения рулоны металла в холодном состоянии прокатывают до нужной толщины: например, с 2-х мм до 0,6 мм. Затем рулоны подвергают смягчающему отжигу в печах и дрессировке – холодной прокатке с маленьким обжатием, чтобы улучшить свойства. Дрессированный металл распускают на ленту или листы. После этого полученную металлопродукцию упаковывают и отправляют потребителю.
В цехе холодной прокатки с металлом так работают две недели. Технологический цикл производства продукции на комбинате – от поступления железорудного сырья до упакованного холоднокатаного металла – составляет 29 суток.
Центральная диспетчерская: контроль за всеми процессами
В центральной диспетчерской комбината в режиме реального времени наблюдают за работой «Запорожстали» – от подготовки железорудного сырья для аглофабрики до отгрузки готовой продукции потребителям. Система также следит за выбросами и возможными внештатными ситуациями, для принятия мер по их исключению.
Система контроля и визуализации, аналогов которой нет на других украинских металлургических предприятиях, – собственная разработка «Запорожстали».
За работой цехов завода удаленно могут следить руководители подразделений с помощью своих мобильных устройств.
Отправка и реализация
Сегодня «Запорожсталь» отгружает порядка 70% экспорта через речные и морские порты Украины. За последние пять лет по воде клиентам комбината отправлено более 2,5 миллиона тонн металлопроката.
ПАО «Запорожсталь» реализует свою продукцию в 60 странах мира. Около 35% продукции комбината продается в Европе.
Текст – Андрей Вавилов, фото – Слава Чиженок
Читайте также:
Как на запорожском заводе готовят квас: экскурсия на производство, — ФОТОРЕПОРТАЖ
Как на запорожском заводе готовят пиво: экскурсия на производство, — ФОТОРЕПОРТАЖ
Как на запорожском заводе делают шифер: экскурсия на производство, — ФОТОРЕПОРТАЖ